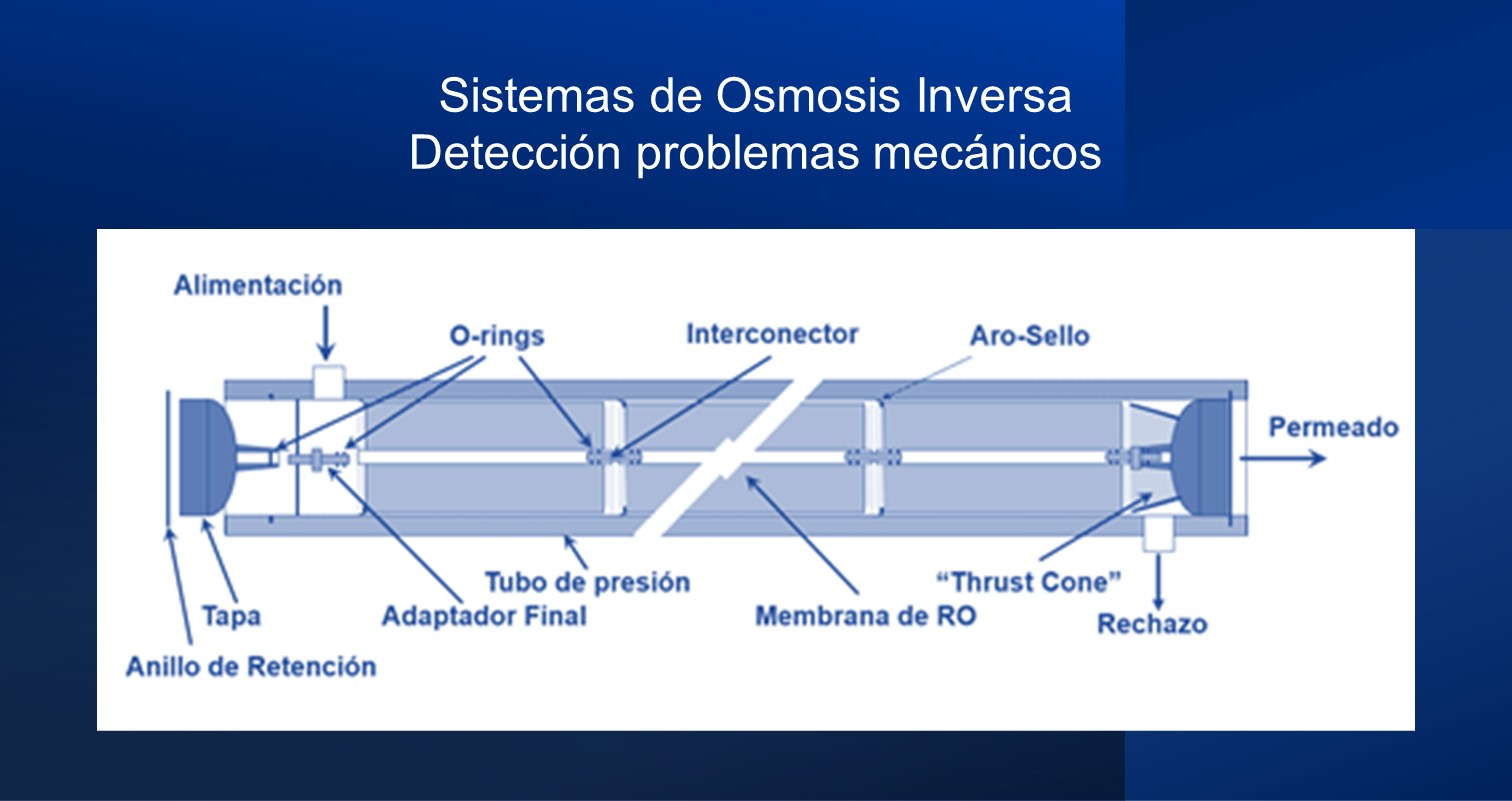
Identificación de problemas mecánicos en sistemas de ósmosis inversa.
Durante la operación de los sistemas de osmosis inversa pueden ocurrir problemas mecánicos de roturas de empaques o interconectores de membranas de ósmosis, estos daños generan paso del rechazo al lado del permeado afectando la calidad del producto final y puede llevar de manera acelerada a un parada de planta.
Identificar la causa y la posición del daño mecánico permitirá dar una solución en menor tiempo evitando extensas paradas de planta, sin embargo, es aún más importante hacer los ajustes necesarios para minimizar los daños mecánicos y de esta manera dar continuidad a la operación, reduciendo los costos operativos y de mantenimiento.
Los daños que se pueden presentar en los sistemas de ósmosis inversa ocurren en las membranas propiamente dichas, o en los elementos que sirven para la instalación de las membranas dentro de los tubos de presión: los interconectores y/o empaques (o-rings).
Las membranas de osmosis inversa pueden dañarse debido a:
- Ataque químico o hidrólisis.
- Afectación de las líneas de pegante usadas para la fabricación de las membranas.
- Daños en la estructura de la membrana por inversión del flujo.
- Abrasión por material externo (arena o material particulado).
- Abrasión por desplazamiento del espaciador de del rechazo.
En este artículo nos centraremos en identificar los problemas en los empaques o interconectores, dejando los problemas de las membranas para futuras publicaciones.
Elementos susceptibles de daño mecánico en los sistemas de osmosis inversa:
Al instalar las membranas dentro del tubo de presión se cuenta con interconectores que unen el tubo central o colector de permeado de una membrana con el tubo central de la membrana aledaña o con los conectores finales por donde saldrá el permeado. Estos interconectores llevan instaladas juntas tóricas u o-rings para aislar el lado del permeado del lado de la alimentación y evitar contaminación.
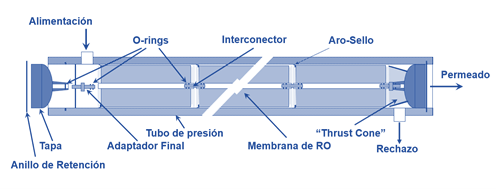
Dentro de estos sistemas, los empaques de los interconectores, o-ring o juntas tóricas son los elementos más susceptibles de presentar daño ya que por su bajo costo se seleccionan materiales que no generen abrasión en los interconectores o tubos de permeado de las membranas, buscando que ante cualquier eventualidad sean los elementos que presenten falla.
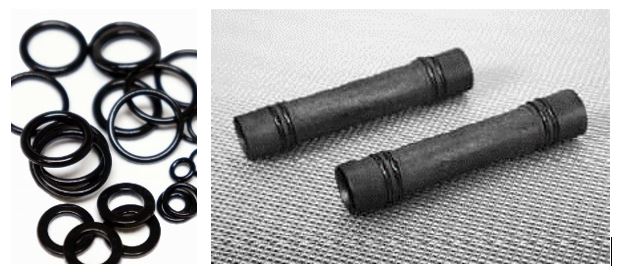
Diagnóstico de los daños mecánicos.
Así como todo tipo de ensuciamiento se puede evidenciar en la variación de parámetros como el flujo, la presión y el paso de sales (conductividad de permeado), ocurre lo mismo con todo daño mecánico en un sistema de ósmosis inversa. En la siguiente tabla se observa el cambio que ocurrirá en el desempeño del sistema cuando se presentan diversos daños mecánicos en los sistemas de ósmosis.
Causa | Cambio en el desempeño | Corrección | ||
Caudal Permeado | Rechazo Sales | Caída de presión | ||
Paso por empaques, aro sellos o tubo central. | Incremento | Disminuye | Sin variación | Reemplazar parte afectada. |
Fuga Membrana por presión inversa (Backpressure) o abrasión | Incremento | Disminuye | Sin variación | Reemplazar Membrana |
Degradación del soporte de la membrana por oxidación | Incremento | Disminuye | Sin variación | Reemplazar membrana |
Degradación del Soporte de la membrana por un solvente | Incremento | Disminuye | Sin variación | Reemplazar membrana |
Incrustación | Disminuye | Disminuye | Incremento | Limpieza, mejorar control de incrustación |
Ensuciamiento Biológico | Disminuye | Sin variación | Incremento | Limpieza, desinfección |
Ensuciamiento Coloidal o Fouling | Disminuye | Disminuye | Incremento | Limpieza, mejorar pretratamiento. |
Ensuciamiento Químicos (Absorción) | Disminuye | Sin variación | Sin variación | Limpieza, mejorar pretratamiento. |
Adicionalmente, la velocidad con que ocurre una variación en los parámetros operativos puede ser un indicio del daño que se ha presentado: el ensuciamiento coloidal puede ser paulatino y ocurrir en el plazo de algunas semanas, el ataque químico producido por un oxidante puede evidenciarse en algunas horas según la concentración del oxidante en el agua y la rotura de un empaque o un interconector puede verse evidenciado de manera inmediata.
Por lo anterior es importante llevar registro de los parámetros operativos y normalizarlos en busca de cambios operativos que no sean evidentes en el corto plazo, e identificar si después de una parada o mantenimiento hubo un cambio en alguno de los parámetros.
Al presentarse un daño en un empaque o interconector el paso de agua del lado del rechazo a la alimentación se reflejará como un incremento en la conductividad del permeado, en algunos casos la conductividad global del sistema seguirá cumpliendo los valores de calidad requeridos. Pero se evidenciará un incremento general en un corto plazo que hará necesaria una revisión más detallada del sistema. En este caso la primera acción que debe ejecutarse es hace un “perfil tubo a tubo”, en el que se muestrea la conductividad para identificar en que tubo se puede estar presentando paso de sales.
Perfil tubo a tubo
En condiciones normales de operación los tubos de presión de la primera etapa tendrán valores de conductividad similares en el permeado, y de la misma forma los tubos de la segunda etapa tendrán valores de conductividad cercano s entre sí. Y siempre la primera etapa tendrá valores de conductividad menores que las etapas subsiguientes.
El perfil de conductividad tubo a tubo consiste en medir la conductividad del permeado en cada tubo de presión, en el ejemplo se muestran los valores para un sistema de osmosis con dos etapas y 10 tubos de presión en la primera etapa y 5 tubos de presión en la segunda etapa:
Condiciones normales | ||
Etapa 1 | Etapa 2 | |
Tubo 1: 113 microS/cm | Tubo 6: 116 microS/cm | Tubo 1: 278 microS/cm |
Tubo 2: 121 microS/cm | Tubo 7: 112 microS/cm | Tubo 2: 285 microS/cm |
Tubo 3: 105 microS/cm | Tubo 8: 122 microS/cm | Tubo 3: 290 microS/cm |
Tubo 4: 109 microS/cm | Tubo 9: 109 microS/cm | Tubo 4: 280 microS/cm |
Tubo 5: 104 microS/cm | Tubo 10: 115 microS/cm | Tubo 5: 292 microS/cm |
Cuando se hace el perfil de conductividad ante el evento de un daño mecánico se puede debe observar un incremento en la conductividad en uno o varios de los tubos. Por ejemplo, en el tubo 7 de la primera etapa:
Daño en el tubo No 7 de la primera etapa | ||
Etapa 1 | Etapa 2 | |
Tubo 1: 113 microS/cm | Tubo 6: 116 microS/cm | Tubo 1: 278 microS/cm |
Tubo 2: 121 microS/cm | Tubo 7: 725 microS/cm | Tubo 2: 285 microS/cm |
Tubo 3: 105 microS/cm | Tubo 8: 122 microS/cm | Tubo 3: 290 microS/cm |
Tubo 4: 109 microS/cm | Tubo 9: 109 microS/cm | Tubo 4: 280 microS/cm |
Tubo 5: 104 microS/cm | Tubo 10: 115 microS/cm | Tubo 5: 292 microS/cm |
En este ejemplo se ha logrado aislar el problema a uno solo de los tubos de permeado, el siguiente paso es identificar que membrana puede presentar el daño. Para esto se debe hacer el sondeo del tubo de permeado.
Sondeo del tubo de permeado
El sondeo del tubo de permeado consiste en insertar una manguera por el tubo central del housing, de manera que se pueda ir extrayendo la manguera aproximadamente 1 metro, que es equivalente a la longitud de una membrana de ósmosis estándar. Y poder tomar una muestra del permeado en el centro de cada una de las membranas. Para el detalle de este procedimiento se deben seguir las recomendaciones de los fabricantes de membranas.
Al registrar la conductividad en cada una de las membranas se puede identificar un incremento súbito en la misma, en el ejemplo en la 4 membrana.
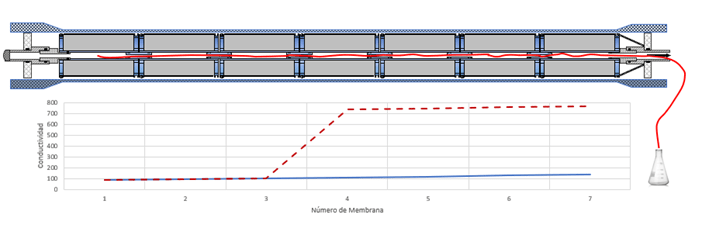
Al realizar este perfil se logra identificar cual es el housing que debe ser intervenido y se pueden prepararlos repuestos necesarios para la intervención.